Principle Introduction
Regenerative Thermal Incinerator (RT0), also known as Regenerative Therma | 0xidizer, is mainly used for the treatment of organic waste gas (V0C) with low to medium concentration and high air volume. The common forms of RT0 equipment include two chamber and three chamber structures, with purification efficiency reaching 97-99%; The purification efficiency of rotary RT0 can reach 99.5%.
System composition
The zeolite molecular sieve adsorption+post-treatment device (RT0) consists of a waste gas pretreatment system, a zeolite molecular sieve adsorption system, a desorption system, a drying and cooling system, a post-treatment system (RT0), and an automatic control system.
Working principle
Efficiently concentrate low concentration high air volume organic waste gas to 10-15 times, heat the concentrated organic waste gas to 760 ℃, and oxidize and decompose the V0C in the waste gas into harmless CO2 and H2O; The heat of the high-temperature gas during oxidation is stored in the heat storage body, which is used to preheat the newly introduced organic waste gas and save the fuel consumption required for heating.
Rotating RT0
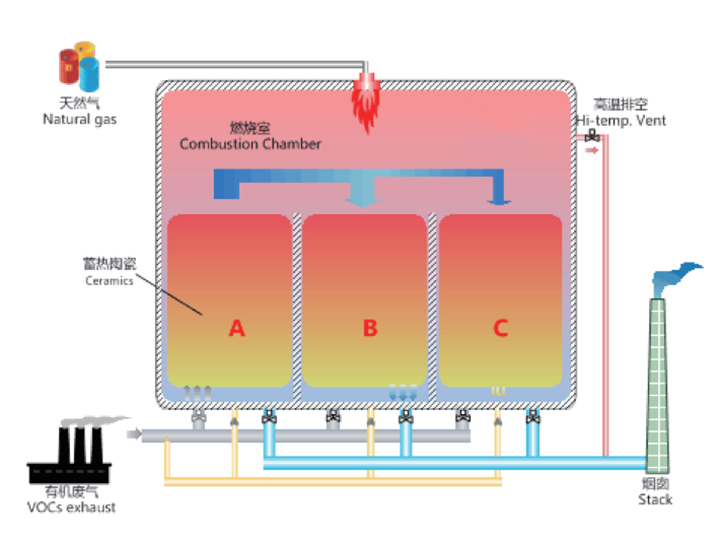
RT0 |
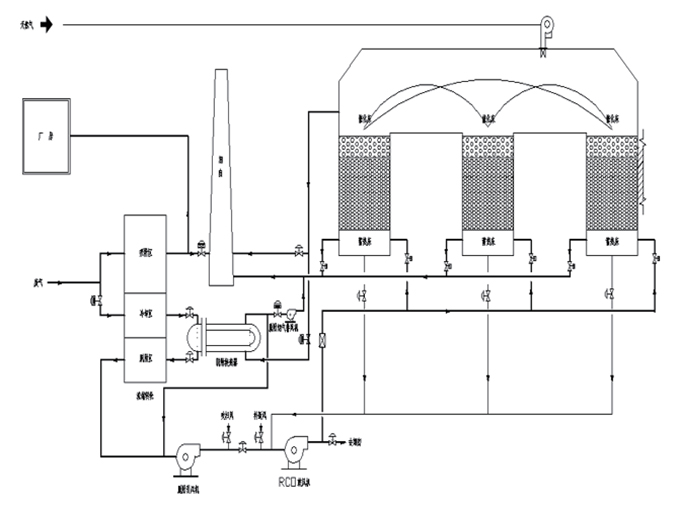
RC0 |
Structure and characteristics
The difference between RT0 and RC0: Simply put, when a catalyst is installed in the RT0 furnace, it is called RC0. Its characteristic is that the catalytic oxidation temperature is around 400 ℃, which can oxidize and decompose various organic compounds to meet emission standards.
Technical principles
The exhaust gas is heated to around 300 ℃ through thermal storage ceramic heat exchange at around 70 ℃, and undergoes flameless combustion reaction at a temperature of around 350 ℃. After combustion, the exhaust gas is cooled to around 110 ℃ through another thermal storage chamber and thermal storage ceramic heat exchange. Organic exhaust gas undergoes oxidation reaction in the combustion chamber, generating CO2 and H2O, which are purified and discharged into the chimney.